The art of good cutting and design

The Good the Bad and the Ugly
Many commercially available gemstones are cut in their country of origin by local craftsmen using primitive and inaccurate machinery. These so called native-cut gemstones are usually cut to maximize yield (= weight of the finished stone) from the rough. This results in stones that in many cases are much less bright than they could be and through which objects below the stone can be seen. Such stones are said to be windowed. Furthermore the nature of the machinery used means that facets cannot be cut accurately and that facets do not meet each other as they should.
​
​
​
​
​
​
​
​
​
A windowed native-cut indicolite tourmaline sent for recutting.
​
In the top images the facets do meet each other and in the image on the left light entering the stone is internally reflected from facets on the bottom of the stone, the pavilion, and all of it is returned to the viewer through the top, the crown. In the middle image the crown is unchanged but the pavilion is too shallow and light is lost through it resulting in windowing and a loss of brightness. The same is true of the stone on the right in which the pavilion is too deep.
​
Using the highly accurate Ultra Tec V5 faceting machine, and after a lot of practice, I cut gems in which all the facets do meet correctly. I also use computer technology to ensure that there is no light loss through the pavilion. As for ultimate brightness, this depends on the material being cut. With many coloured stones the depth of colour may be a primary consideration and achieving optimum brightness may detract from this meaning that a compromise must be reached. Creating or modifying designs and accurate cutting to produce the most beautiful gem possible from the available material is the ART of cutting faceted stones and the design process can often take as long and be as rewarding as the actual cutting.
​
​
​
​
​
​
The stone after recutting to the design below. This design, as with many long thin designs, produces a small "bow tie", the dark vertical lines in the middle of the stone seen from some viewing angles, but this is a small price to pay for the transformation.
​
​
​
​
​
​
​
​
​
​
​
​
​
​
​
​
​
​
​
​
​
​
​
​
​
​
​
​
​
​
​
​
This "simple" design is far from simple to cut. It came about out of a desire to produce good optical performance while retaining as much of the original stone as possible. Here is another for Tourmaline, this time for a shallow native-cut pink stone to go into an antique ring. The cut is relatively straightforward but the amount of material available left no margin for error.
​
​

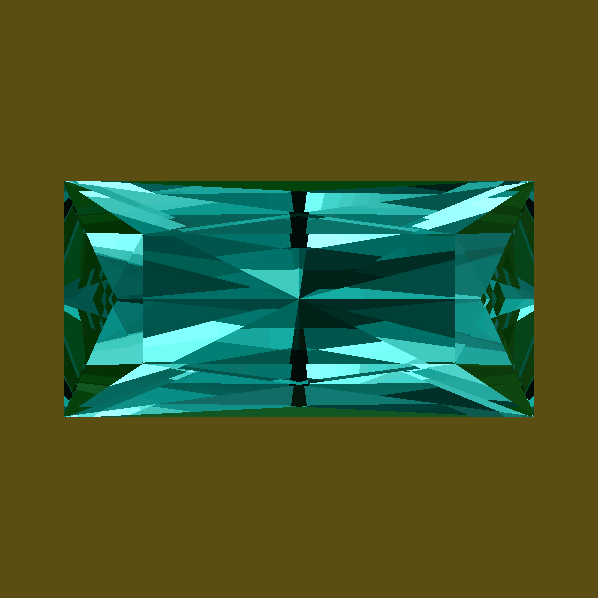



Corundum and CZ
Pendant
Natural tourmaline
CZ and corundum
Pendant


My first designs were produced using the Windows-based computer aided design software GemCad and optical performance optimized using the sister program GemRay. Both were created by Robert Strickland and can be downloaded from www.gemcad.com. However, in the autumn of 2018 another design package was launched by Rej Poirier. This is the revolutionary Gem Cut Studio (GCS) available in both Windows and Mac formats. Having 'grown up' with GemCad and only having had a few hours to work with GCS I still find the design process easier using GemCad, although it took me a long time to get to grips with it. I have a feeling that GCS will eventually prove to the more intuitive design software but from the outset it is its gem optimization features that particularly attract me to this design suite. They are superb. See a brief note on the News page here. These features make the artistic side of gem design a real pleasure and the results can be exported in either GCS format or in GemCad format making designs available to all.
Spinel ring

s@mys.uk.com +447860 499851
